Ensuring Safety and Reliability in Electrical Systems
At Electrical Safety UK (ESUK), we are dedicated to providing comprehensive solutions for arc flash prevention, ensuring the safety and reliability of your electrical systems.
By partnering with ESUK, you benefit from our commitment to safety, innovation, and expertise in arc flash prevention. We help you create a safer working environment, reduce risks, and ensure the longevity and reliability of your electrical systems.
Would you like more details on any specific aspect of our services?
Live working
When working on electrical systems, the equipment should be de-energised, isolated, locked and labelled wherever possible. Electrical systems should be designed to eliminate energised work as much as possible. Consideration should also be given to segregation of power and control circuits, test points and shrouding and insulation to ingress protection level 2X (finger safe).
Electrical Protection System
The design of electrical systems focused on arc flash risk reduction can utilise the following to help minimise the risk of exposure to elevated arc flash incident energy levels:
- Remote switching
- High/Low impedance bus differential protection
- Fast acting earth switches
- Current limiting devices
- Arc flash detection relays
- Arc rated equipment
- Maintenance settings for protective devices
On typical industrial and commercial private electrical networks in the UK the high voltage (above 1000Vac) part of the network has voltages up to 11kV. These networks are commonly found in factories, commerical buildings and other high energy use locations. At ESUK we have carried out hundreds of arc flash studies on these types of networks and we often find that the arc flash hazard or incident energy levels are higher on the low voltage parts of the network than the high voltage parts of the network. Also, we find that there are more pieces of equipment on the low voltage network with incident energy levels >8Cal/cm2. It is also common to find high levels of incident energy immediately downstream of the transformers supplying the LV network. In the example below we can see we have only 1.1Cal/cm2 on the high voltage side of TX-1 and 22.7Cal/cm2 on the low voltage side of TX-1.
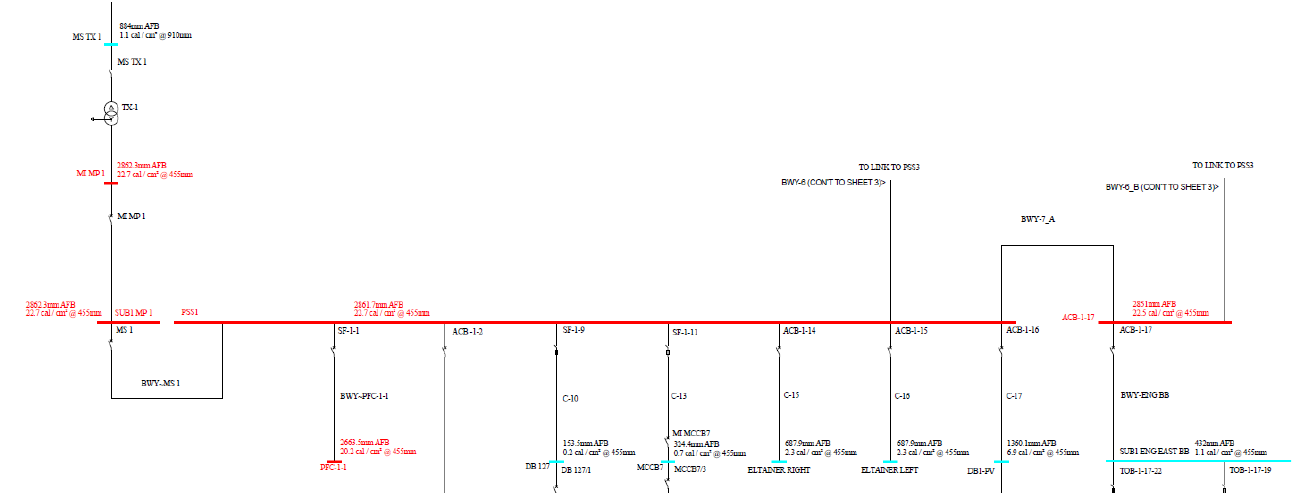
On existing legacy electrical networks we often advise our clients to make changes to their protection settings to reduce the arc flash hazard. Bear in mind that incident energy levels are a function of short circuit fault current and the disconnection time of the upstream protective device. So in the example above if the circuit breaker MI MP 1 has an instantaneous setting that can be adjusted it may be possible to reduce the incident energy on SUB1 MP 1 by reducing the time it takes MI MP 1 to open if an arc flash occurs in it’s zone of protection.
Minimisation of incident energy levels may be achieved by looking at trip times or fuse ratings and exploring possibilities for faster disconnection times. This may be a temporary measure for work on a particular piece of equipment by lowering the instantaneous protection settings to a minimum. These temporary settings are often referred to a “Maintenance Settings”. The following example shows how the instantaneous setting may be moved to lower the instantaneous pick-up time.
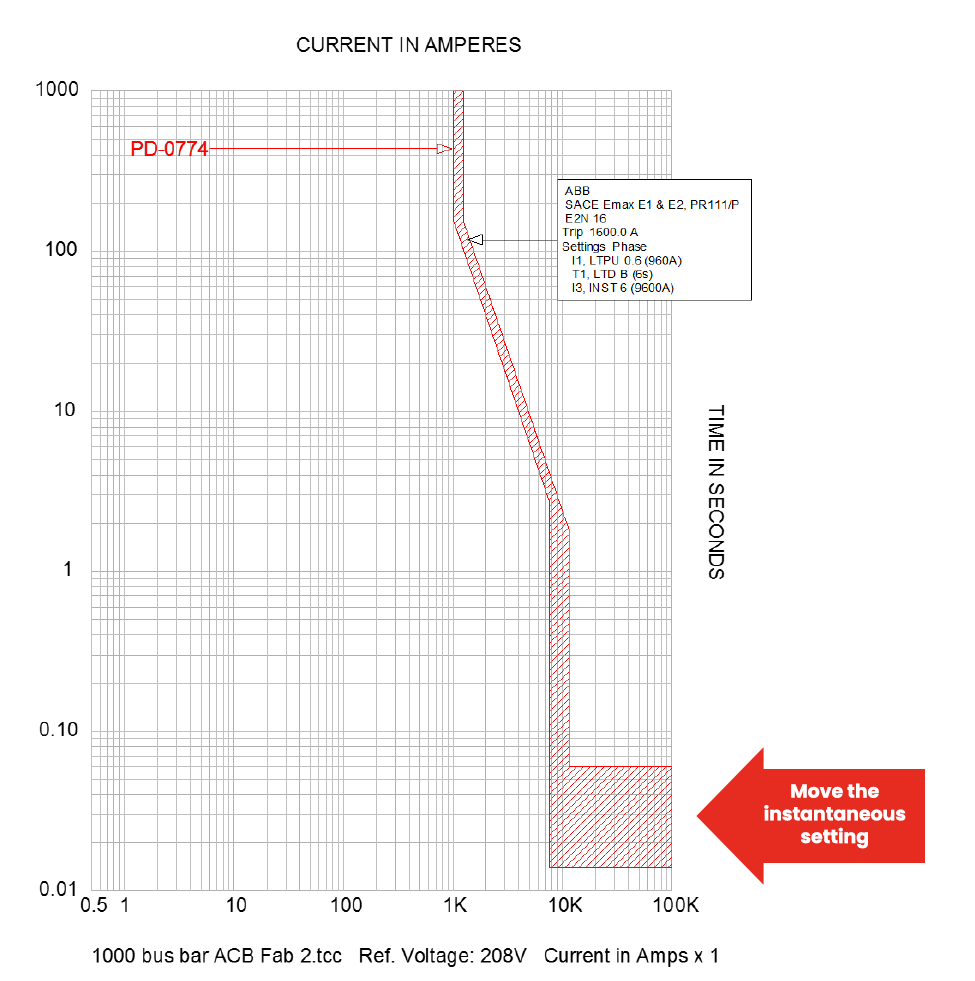
The incident energy is not dependent upon fault level only and the paradox is that in many instances lower levels of prospective short circuit current may actually prolong operation of protective devices and increase energy let through. It should not be assumed that the incident energy levels will reduce as you come down the network towards the final circuits.
Inspection, Test and Maintenance
Finally, proper maintenance of electrical equipment plays a part in preventing arc flash events. Keeping your equipment in good condition and using predictive techniques such as thermography (LV equipment) and partial discharge monitoring (HV equipment) can detect failures before they become catastrophic.
We often find that electrical enclosures which were originally designed to be finger safe, can over time become degraded. Shrouding, covers and insulation can be removed and not refitted or damaged during maintenance. It is a good idea to make sure that your instructions for maintenance include a visual inspection to check that the IP2X protection level has not been degraded.
Inspection and testing of protective devices is essential to ensuring that they will work correctly if called upon to operate under fault conditions. Unrevealed failure mechanisms may not be apparent under normal operating conditions, so it is essential that maintenance activities are carried out at appropriate time intervals to detect and correct these types of failures.